Era tempo che pensavo di realizzare un nuovo preamplificatore a valvole. Ho avuto già esperienze nella realizzazione di tale tipologia di apparecchi. In particolare ho “tentato” di realizzare il PST200 di Aloia partendo dagli schemi pubblici. Ma il risultato non è stato esaltante. Sarà la tipologia utilizzata (totem pole), sarà il fatto che era la mia prima esperienza “complicata”, ma il suono non era all’altezza della situazione. Di fatto, l’ho smantellato e messo da parte. Dopo vari consigli avuti da altri appassionati in giro per forum, mi sono buttato a capofitto in un progetto completamente diverso. Una replica del famosissimo Conrad Johnson PV10.
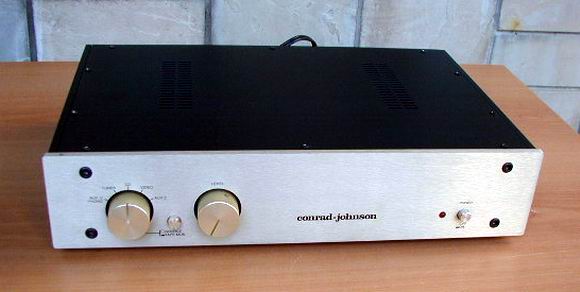
Molti ne parlano bene per il suono, legato forse al tubo utilizzato, ECC82, e alla tipologia circuitale adottata. Un classico dei pre valvolari anni 90.
Uno dei tanti siti che trattano di questo preamplificatore è questo: http://www.cma4ch.org/chemo/attivita/CJpv10.html dove ci sono foto, schemi e anche consigli per migliorie e upgrade.
Si inizia dallo schema elettrico, cosa fondamentale per iniziare lo studio e vedere se la cosa è fattibile. Da una prima analisi noto subito la caratteristica tipica degli schemi dei “valvolari”. La parte alto livello molto semplice, alimentatore molto complesso e critico.
L’alimentatore, nei valvolari, (in base alle mie piccole esperienze) è sempre critico perché in queste tipologie il rumore è un problema molto sentito, e se questo è presente nell’alimentazione si ribalta in uscita, anzi si ribalta “amplificato” con risultati finali veramente scadenti. Quindi massima attenzione nei circuiti di alimentazione.
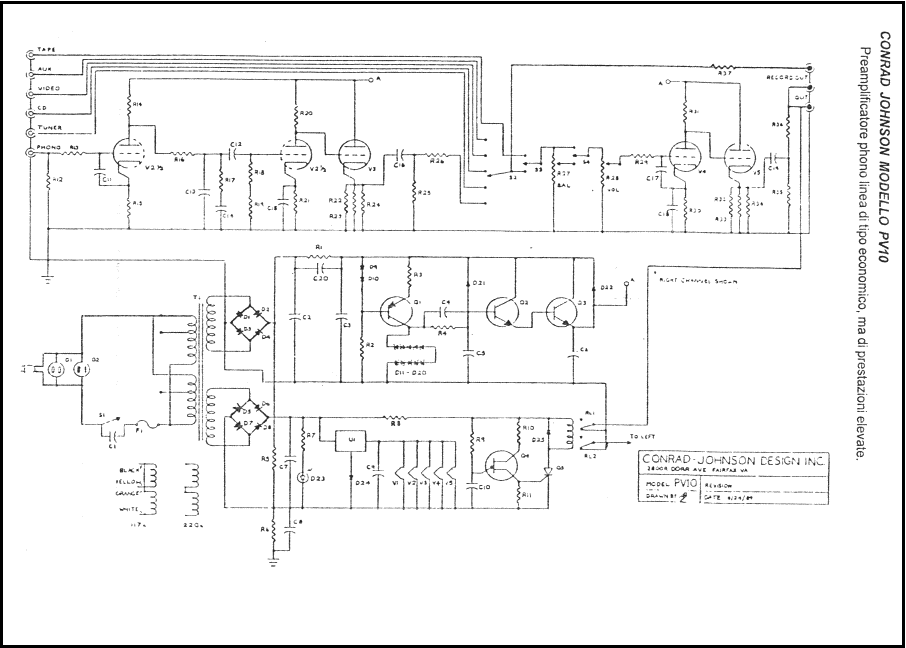
Per semplificarmi la vita ho deciso di puntare sulla versione senza stadio phono. (sigla PV10L)
Non ho quindi considerato per niente lo stadio phono, anche perché di solito è il più difficile, sia per i componenti che per la messa a punto dello stampato. Valuterò in seguito se aggiungerlo come upgrade al progetto.
Lo stadio di linea ad alto livello è molto semplice, 2 triodi ECC82 montati in configurazione catodo comune.
Più complesso è l’alimentatore, come tutti valvolari, formato da due sezioni. Una per l’alimentazione dei filamenti, a bassa tensione (12v), l’altra per l’anodica da circa 300v.
La parte filamenti è realizzata con un classico 7812, nella versione “metallica” ovvero TO3,
più difficile da trovare in giro, ma per fortuna presente nei cataloghi dei fornitori web.
La parte alta tensione si sviluppa intorno ad un circuito stabilizzatore realizzato con diodi zener e transistor.
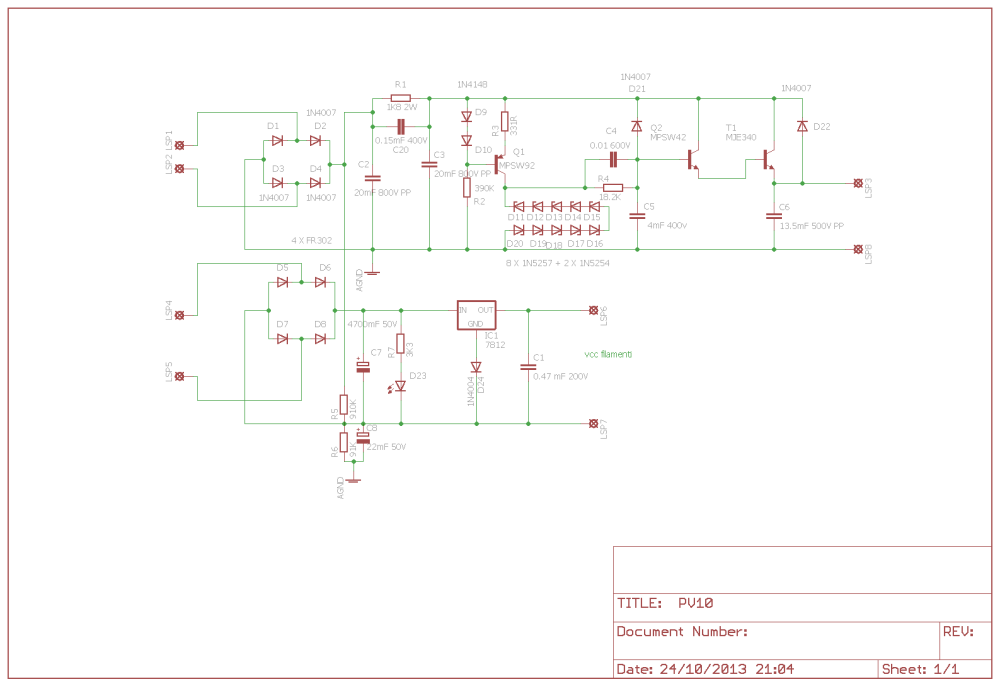
Scheda alimentatore
L’alimentatore presenta subito un problema di realizzazione. La sezione HT non fa uso di condensatori elettrolitici, ma SOLO condensatori non polarizzati. Quindi polipropilene, per alta tensione che hanno dimensioni “importanti”. Comincia la ricerca. Se fosse stata vana il progetto sarebbe “finito” prima di iniziare.
Fortunatamente su internet ho trovato i Murdorf, ottimi condensatori moderni, in polipropilene, con valori di tensione compatibili con i progetto. Alcuni appassionati su internet li hanno utilizzati per sostituire gli originali su apparecchi storici.
Ho scelto gli M-CAP classici con tensioni da 630V. Ne occorrono ben quattro, con un occupazione di spazio notevole e peso consistente.
Nella lista dei componenti dell’alimentatore ho trovato altri componenti critici, i transistor utilizzati nello stabilizzatore. La coppia MPSU10/MPSU60 risultava difficile da trovare. Li ho sostituiti con MPSW42/MPSW92, componenti equivalenti di facile reperibilità.
Dallo schema originale ho buttato giù gli schematici su EagleCad per la realizzazione degli stampati.
Ho controllato i componenti, sulla rete si trova anche la lista dei componenti ufficiale, uno per uno e verificato i valori. Ho controllato il foot print, ovvero l’ingombro fisico, infine ho stilato la mia lista dei componenti composta dai codici reperiti tra i vari fornitori web.
Per i condensatori non polarizzati e il contenitore Hifi2000 mi sono rivolto ad AudioKit, per il resto dei materiali ho scelto RS Components. Per il contenitore ho scelto una cosa semplice e standard, SlimLine da 2 unità con frontale e controfrontale. (poi vedremo perchè)
Per la realizzazione dell’alimentatore ho creato una unica PCB per BT e HT. Sulla parte superiore la sezione di BT. Ho utilizzato il regolatore in contenitore metallico (versione K / TO-3) come da progetto originale.
Nella parte bassa del pcb troviamo la parte HT, con i due condensatori posti dopo il ponte raddrizzatore e la “griglia” di zener stabilizzatori.
Appena avuti i componenti ho proceduto al montaggio delle schede, testando i componenti uno per uno prima della saldatura. Partendo come sempre da quelli più “bassi” (resistori, diodi, zoccoli) e finendo con quelli più ingombranti.
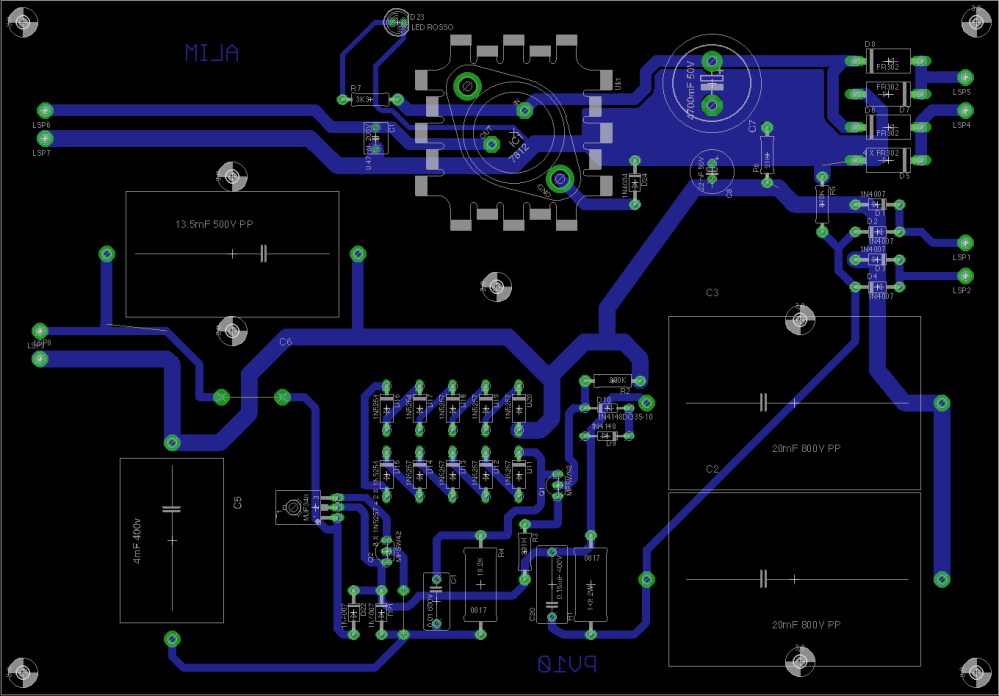
Da notare i fori supplementari per il bloccaggio dei condensatori con fascette. La scheda è imponente e occupa quasi tutto il contenitore.
Altro problema da superare è il trasformatore di alimentazione. L’originale è un tradizionale trasformatore a lamierini. Io per motivi di spazio ho deciso di utilizzare un toroidale, devo utilizzare un trasformatore di diametro massimo 80mm per poterlo montare in verticale su un contenitore da due unità.
Per la sua realizzazione mi sono appoggiato ad una azienda marchigiana che realizza trasformatori custom su specifica. Per i test iniziali ho utilizzato un trasformatore a lamierini che avevo in casa, esterno al case.
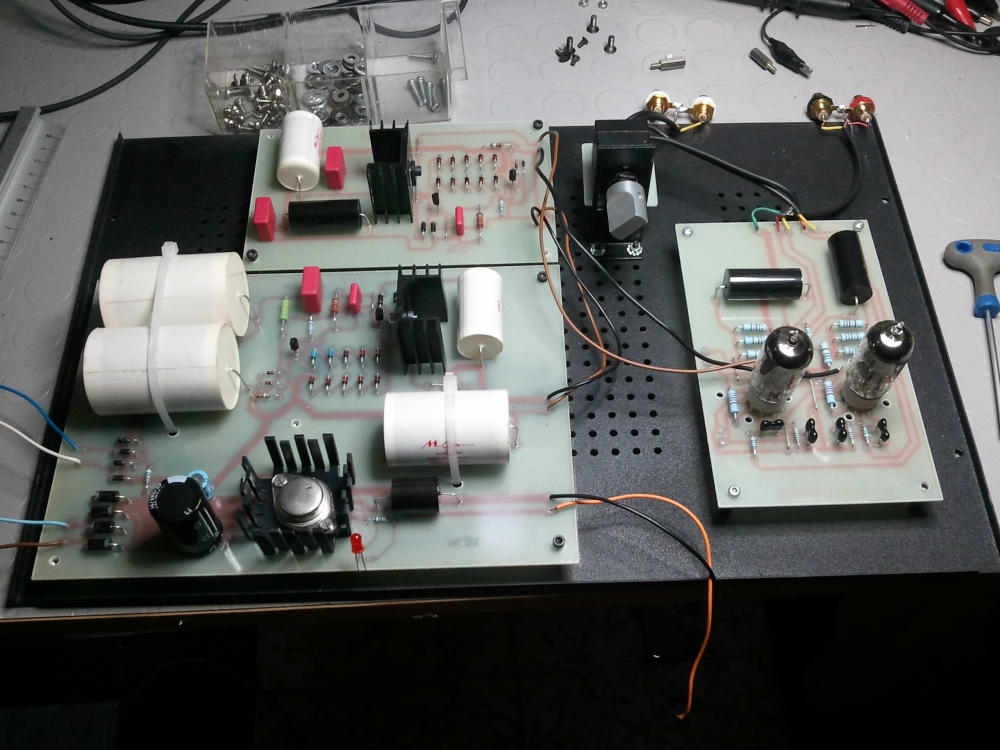
Scheda preamplificatore alto livello.
Ho realizzato lo schema al CAD e poi ho cominciato a studiare il circuito stampato.
Per la realizzazione di questa scheda ho analizzato il progetto originale, mediante foto trovate in rete, in modo da avere un riferimento per il posizionamento dei componenti.
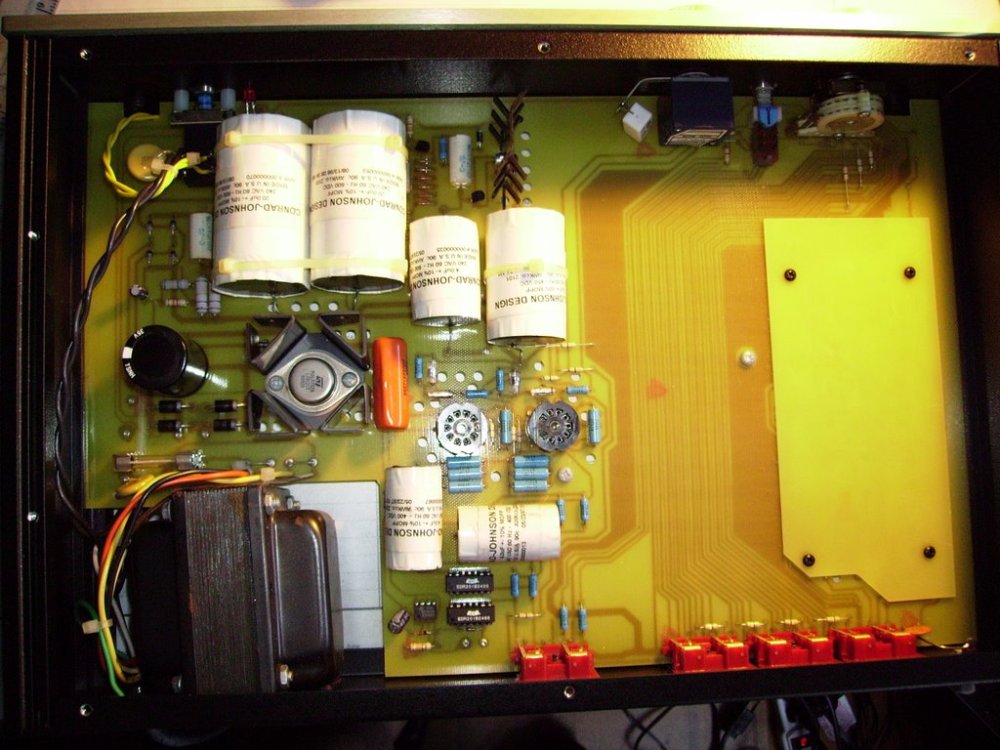
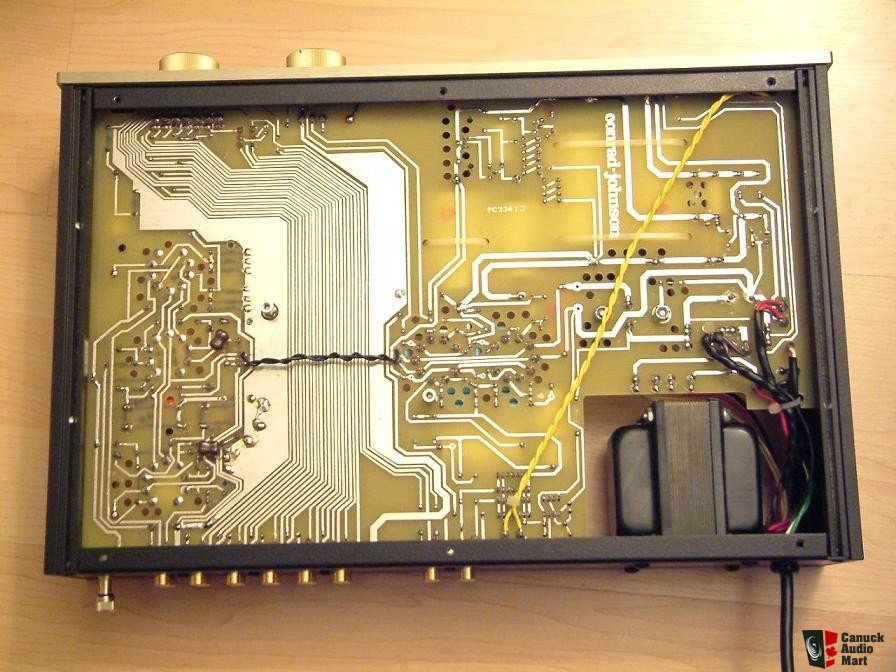
Anche qui non ho fatto economia di spazio, la scheda è da 100×160. Questa abbondanza di spazio mi permette di distanziare i componenti in maniera da migliorare la dissipazione del calore prodotto dai tubi. Per lo stesso motivo vicino ai tubi ho previsto alcuni fori da 3mm per permettere un miglior passaggio dell’aria tra le due facce del PCB.
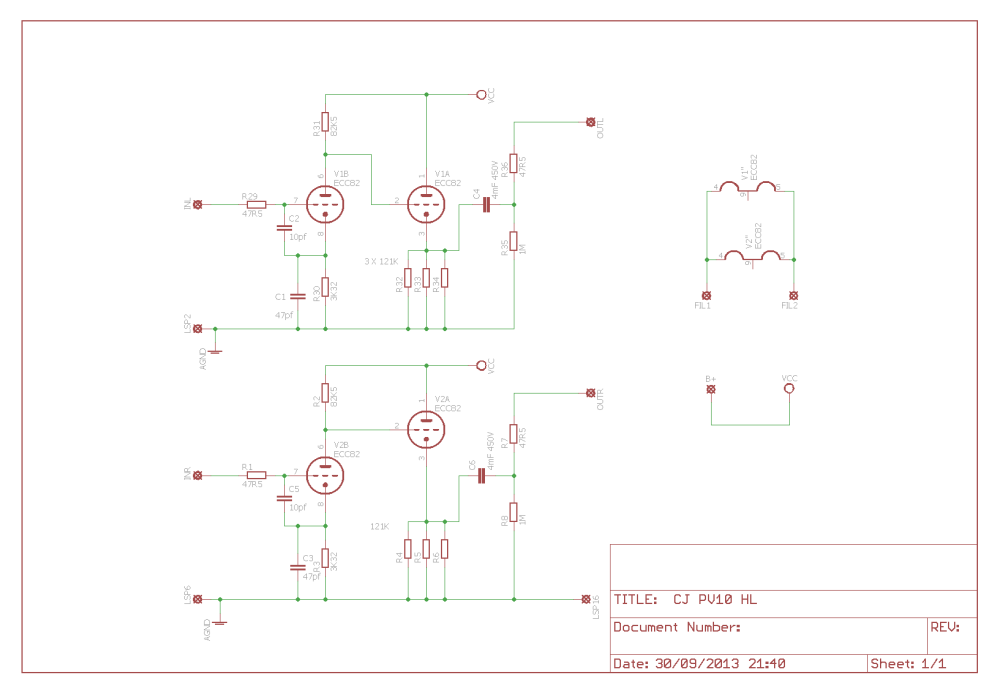
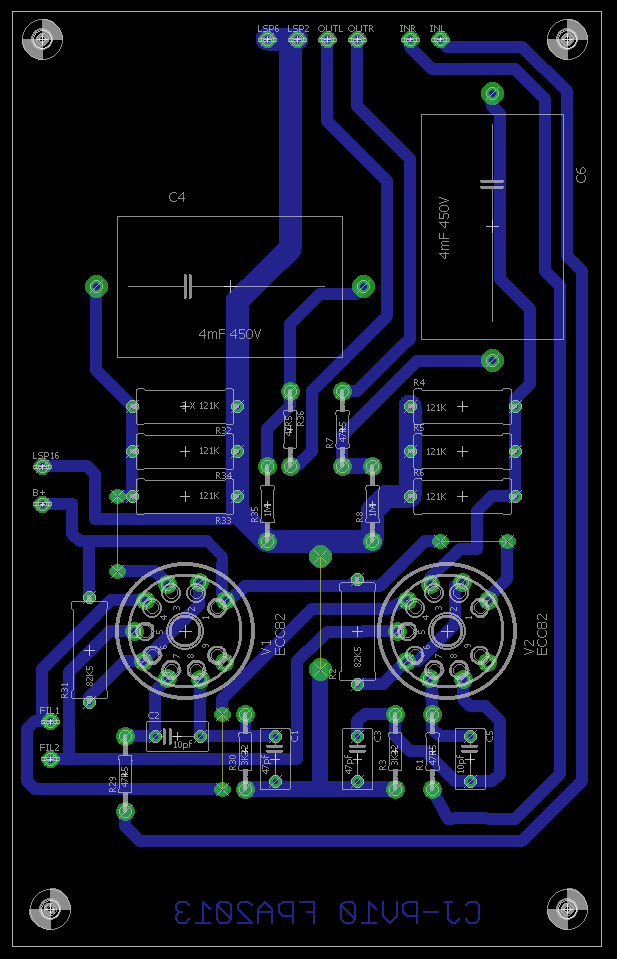
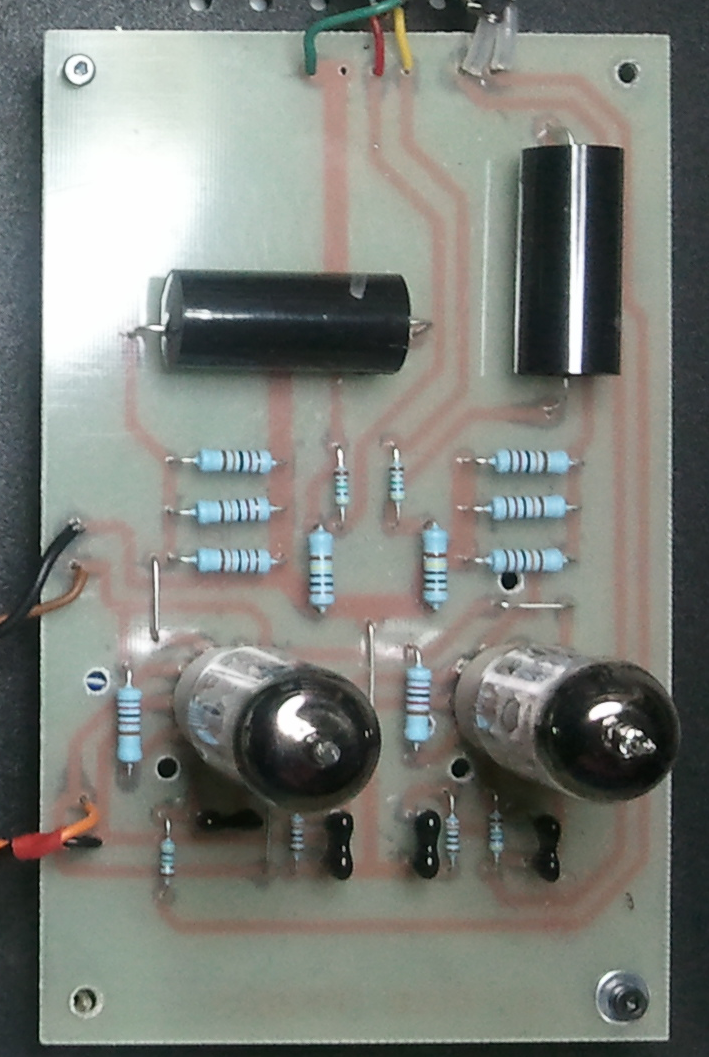
Primi test sul banco
Bene, ho realizzato la scheda alimentatore, la scheda alto livello, possiamo fare qualche test per vedere se il lavoro è andato come si sperava.
Montate le schede e fatto i collegamenti, ho effettuato dei test con oscilloscopio e generatore di segnali. Ho fatto anche dei test con un PC e VisualAnalizer per vedere come si comportava sull’analizzatore di spettro.
Le prime prove hanno avuto esito positivo. Mi ha fatto un po’ “impazzire” il discorso dei collegamenti, in particolare, l’eliminazione del rumore da ground-loop. Mi sono studiato lo schema originale, ed ho creato un centro stella sull’alimentatore dopo il raddrizzatore dei filamenti, vicino ai condensatori di livellamento.
Inoltre ho dovuto realizzare un piccolo PCB per montare il potenziometro del volume. Un “Noble” da 100k che ho in casa da molti anni e che custodivo gelosamente.
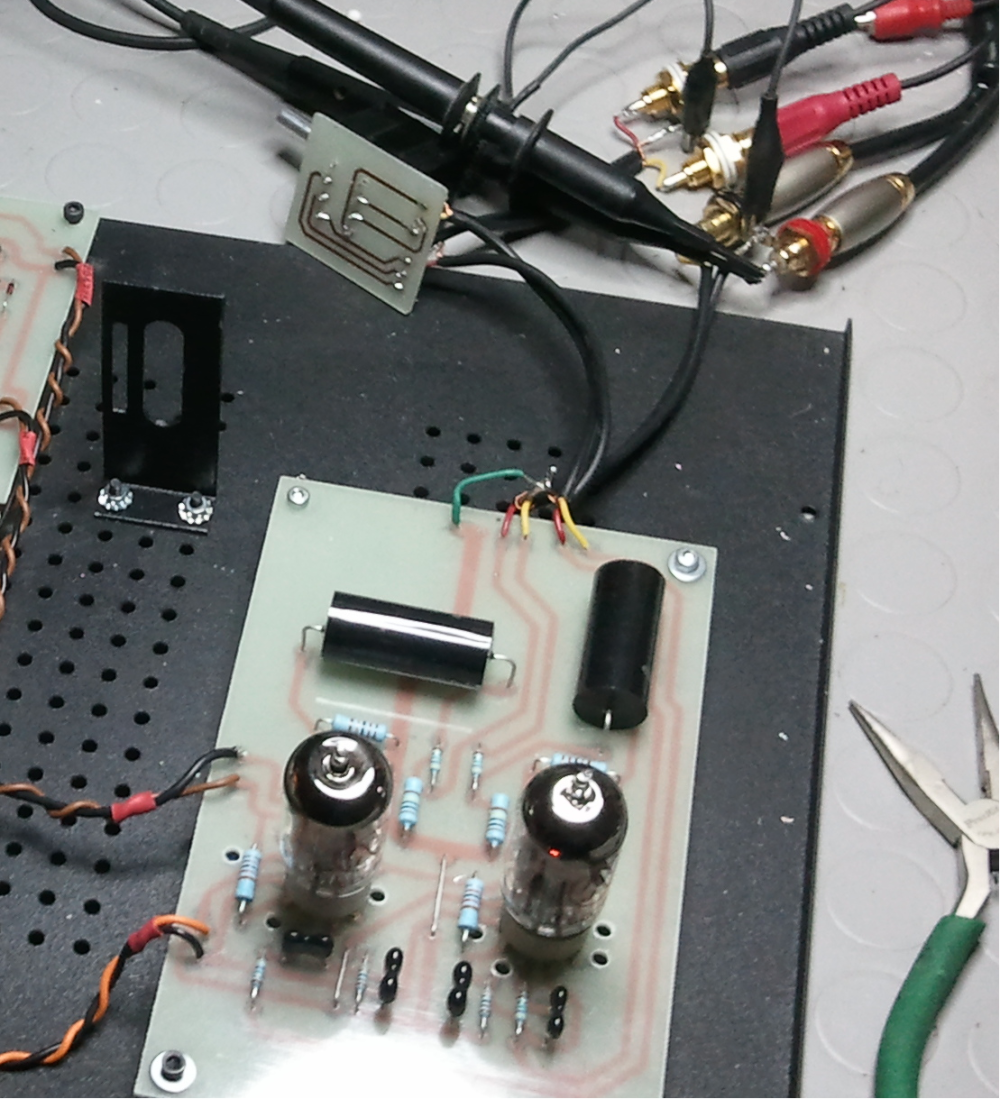
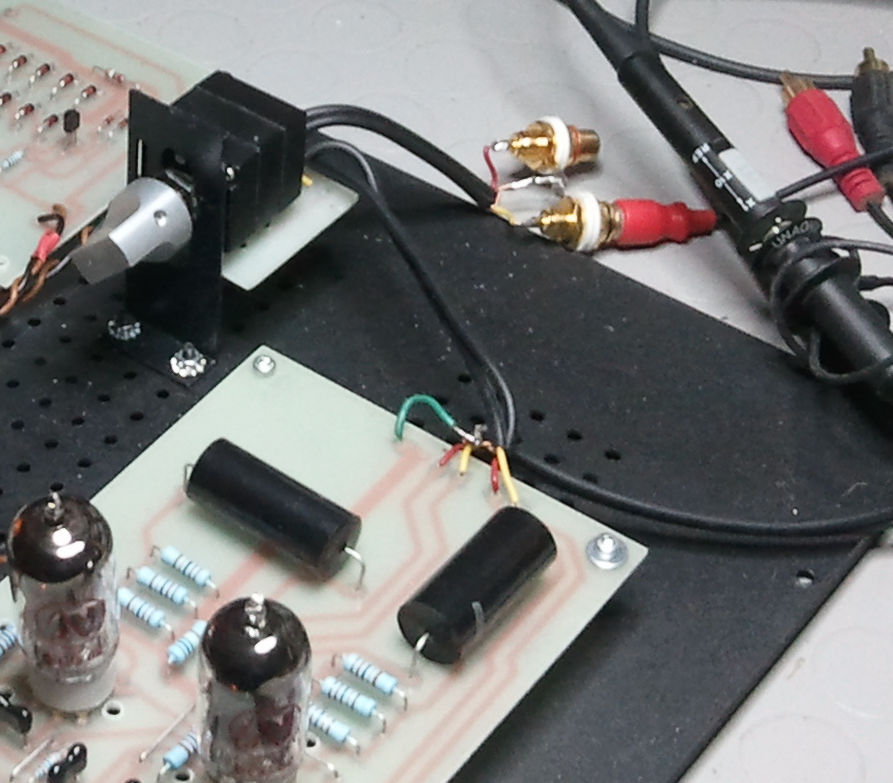
Ecco uno scorcio del Lab con le schede in test.
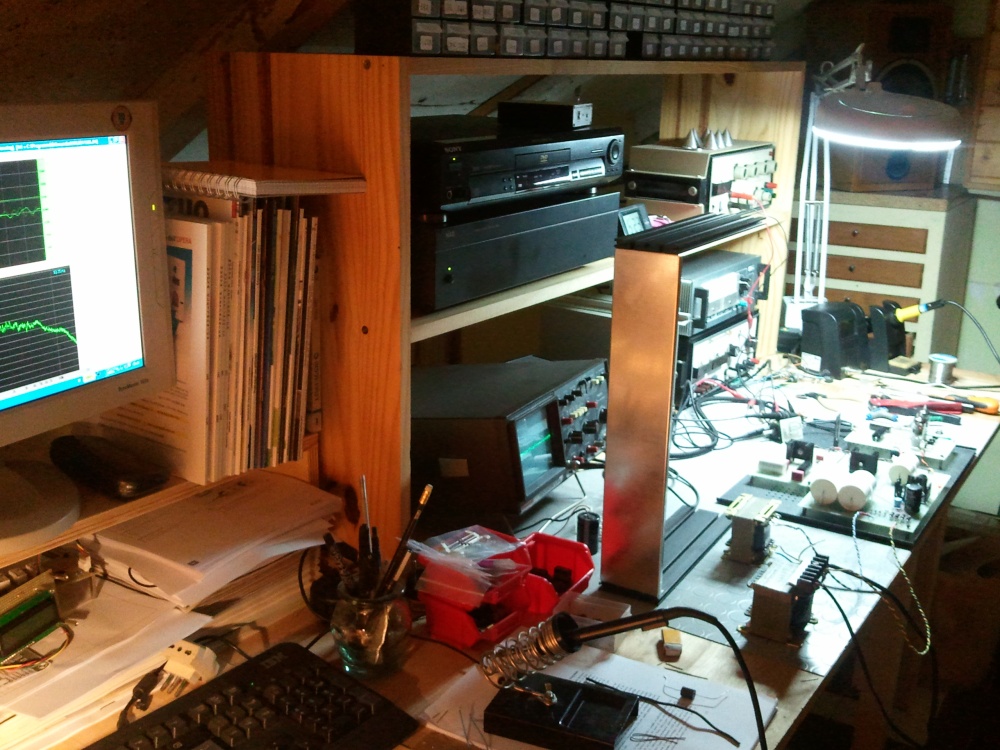
Manca ancora qualcosa
Si, manca ancora qualcosa. Per far si che il preamplificatore sia operativo occorre anche un selettore di ingressi, che permetta all’utente di selezionare le varie sorgenti. Inoltre nel progetto originale è presente anche un circuito di ritardo per l’attivazione dell’uscita.
Questo circuito serve ad eliminare i “rumori” causati dall’accensione dei tubi. Un timer con 555 fa scattare un relè dopo circa quaranta secondi per permettere ai tubi di andare a regime.
Ho quindi creato un PCB, da collocare vicino i connettori d’ingresso, per permettere la selezione delle sorgenti. Questa scheda è poi collegata, mediante un cavo, al commutatore posto sul pannello frontale. Su questa scheda ho inoltre implementato il circuito di ritardo, posto subito dietro i connettori di uscita.
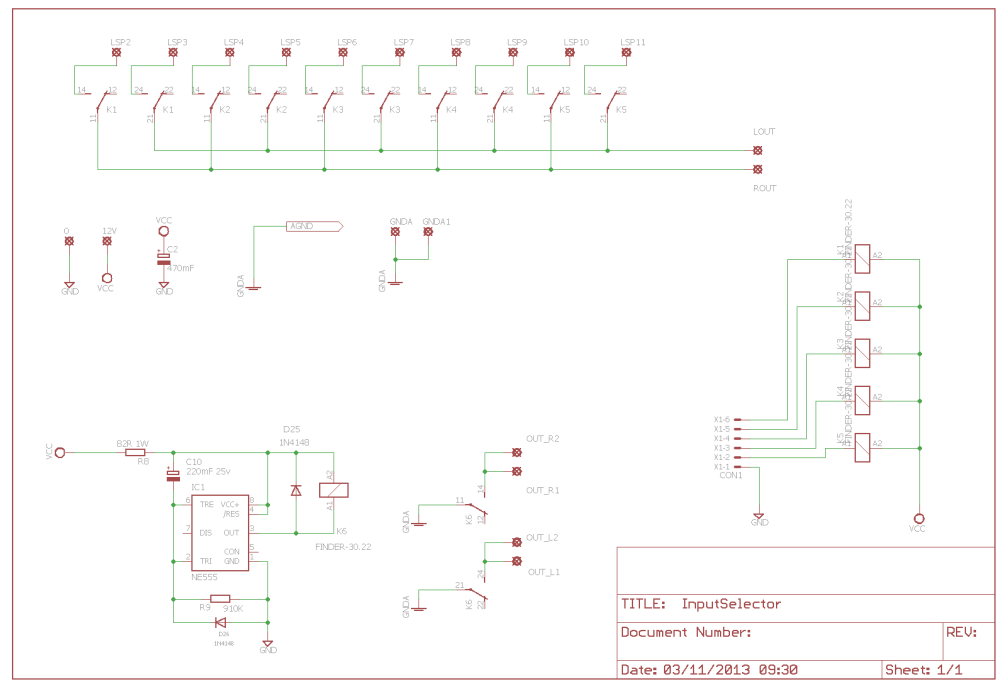
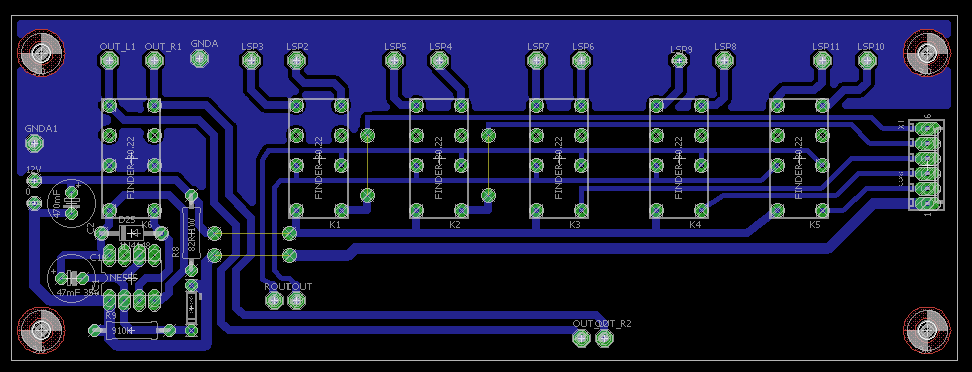
Upgrade
Ho fatto diversi test sul prototipo, soprattutto di ascolto. La cosa era buona ma non mi convinceva. Allora ho fatto delle ricerche sui vari forum e siti di hifi dove si parla di Conrad Jonson. Da questo ho capito che un ulteriore miglioramento era possibile modificando lo stabilizzatore anodico. Infatti la stessa “casa” aveva successivamente lanciato l’evoluzione del PV10 ovvero il PV12 che aveva come caratteristica un alimentatore anodico “potenziato”. L’alimentazione anodita o HT in un valvolare è fondamentale per il suono, più è pulita e migliore è il suono. Nei vari siti visitati sono rimasto affascinato dal lavoro fatto da un certo Nigel Tufnel (http://pqltd.blogspot.it/2006_08_01_archive.html) dove al suo CJ PV10 ha aggiunto un ulteriore stabilizzatore anodico trasformandolo, di fatto, in un CJ PV12.
Il PV12 era praticamente un evoluzione del PV10, ed aveva appunto un alimentatore anodico con uno stabilizzatore aggiuntivo per ogni stadio (phono e linea).
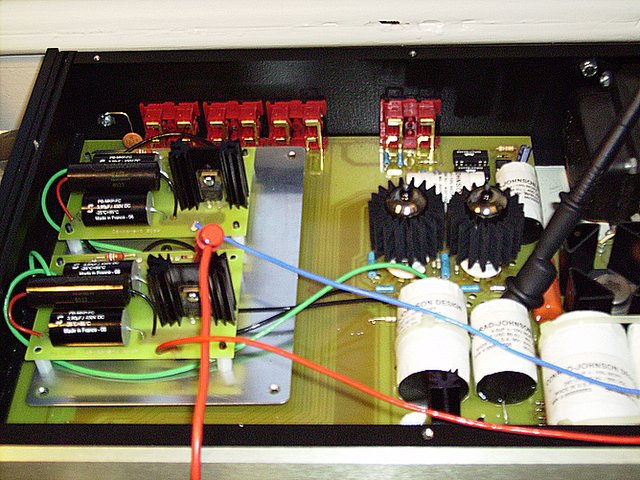
Dallo schema di Nigel ho realizzato una nuova PCB da aggiungere all’alimentatore principale.
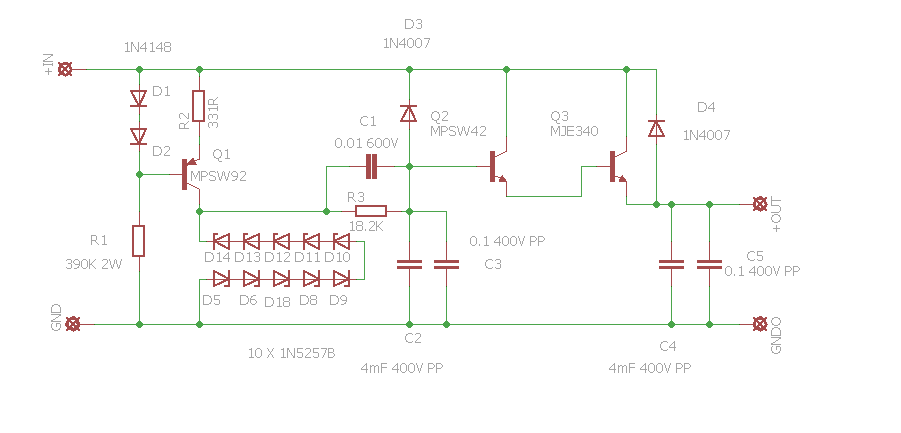
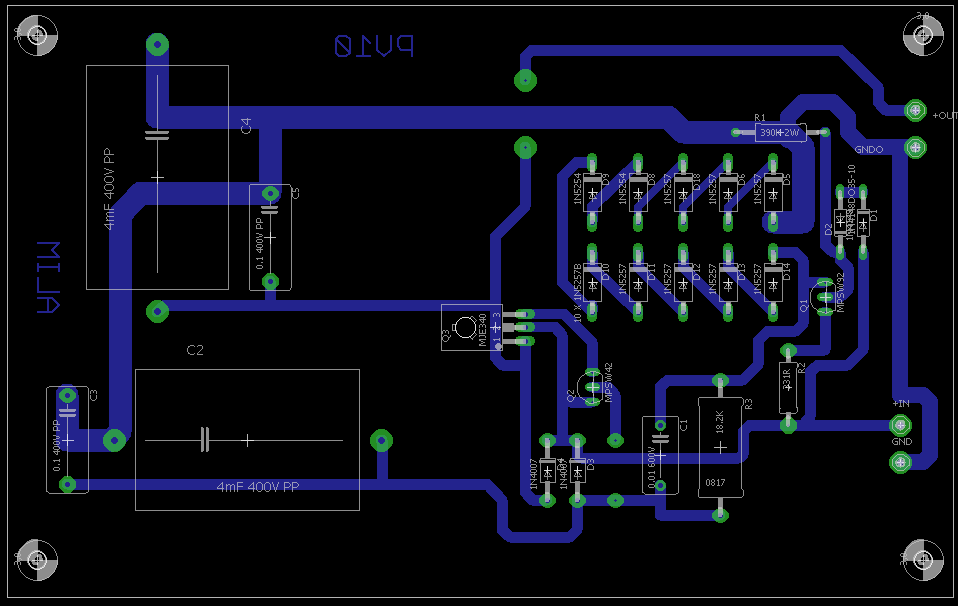
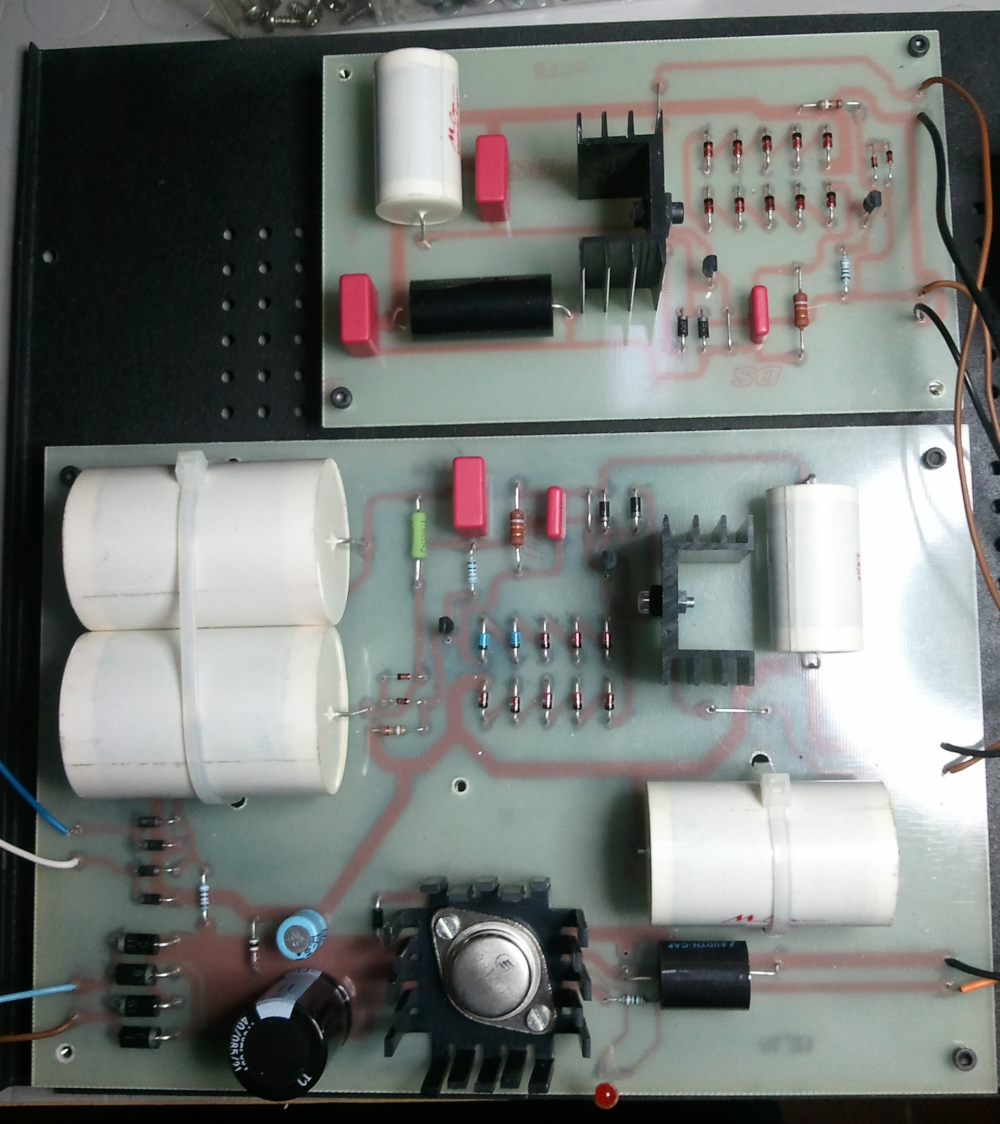
Messo al banco di prova il prototipo ha subito mostrato un miglioramento nel suono.
Il suono molto più pulito e dettagliato. Anche i test con VisualAnalizer hanno evidenziato una diminuzione del livello di rumore di fondo.
Bene è il momento di passare alla fase di assemblaggio meccanico.
Assemblaggio
Si parte dalle schede. Per prima cosa ho installato le schede sul fondo con delle torrette.
Per il posizionamento ho usato un mio metodo standard. La parte alimentazione nel lato sinistro mentre la parte alto livello e ingressi nel lato destro.
Per l’organizzazione del pannello posteriore ho utilizzato il CAD per simulare il pannello e avere le quote di riferimento. Ho stampato il piano di foratura su un foglio in scala 1:1, ho poi sovrapposto il foglio al pannello e tramite “bulino” ho fatto i segni per la foratura. Fatte le forature, proteggendo prima il pannello con del nastro gommato, ho poi montato i pin RCA, il portafusibile e il portacavo con il cavo di alimentazione.
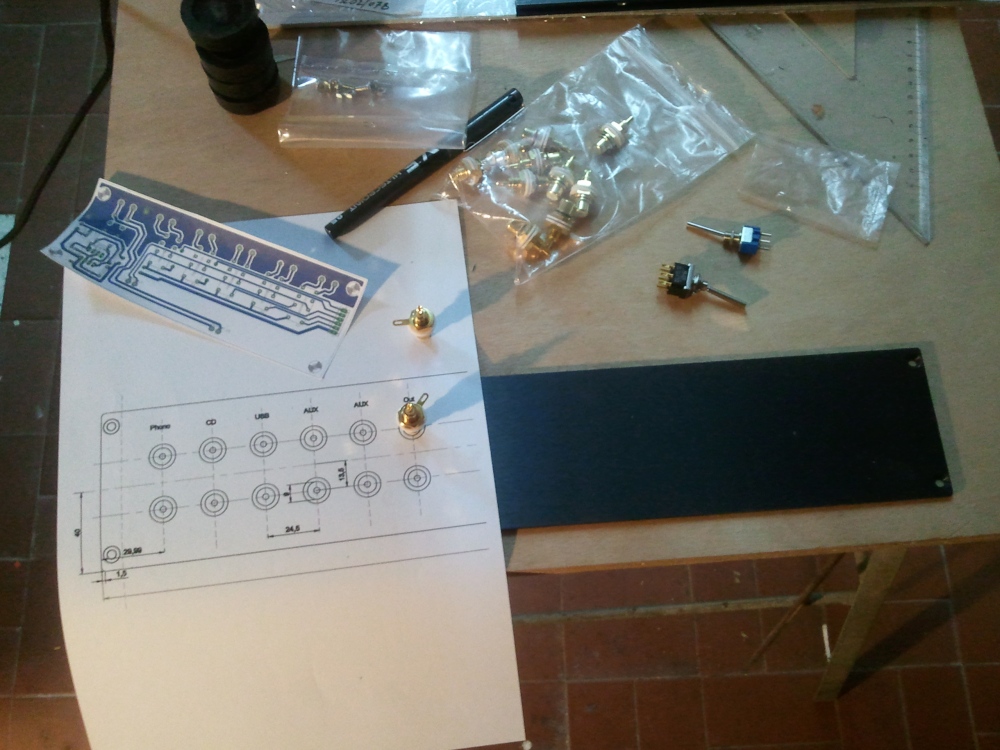
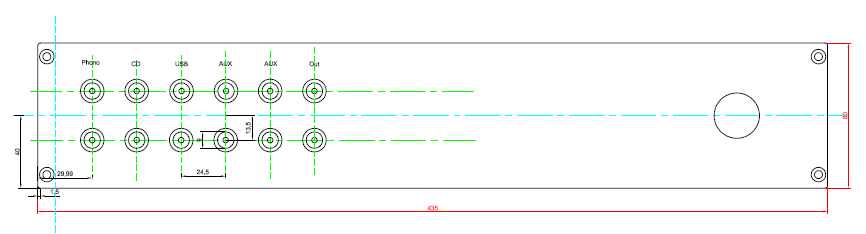
Per il pannello frontale ho utilizzato lo stesso metodo. Dal piano di foratura ho segnato il pannello. Ho fatto dei fori guida da quattro millimetri. Poi ho montato il pannello sul contenitore a contatto con il contropannello e ho riportato i fori guida sul contropannello.
Ho fatto le forature del contropannello e ho montato lo switch, l’interruttore di accensione, il led e la boccola guida per l’albero del potenziomentro. Il pannello frontale di alluminio l’ho lasciato per ultimo. Ho allargato con fresa a tazza i fori per le manopole (sono da 25mm), e i fori dell’interruttore e del led.
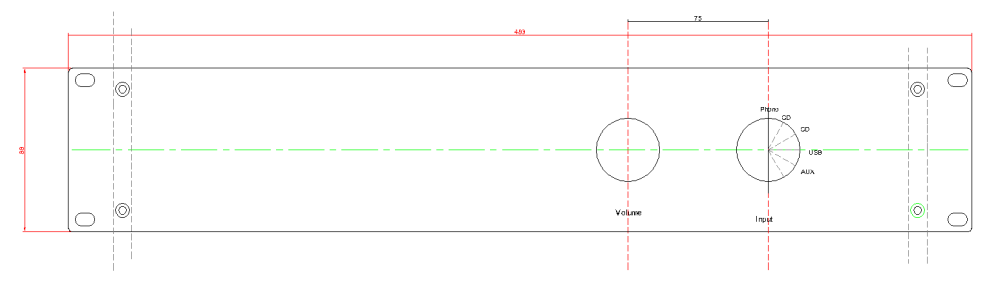
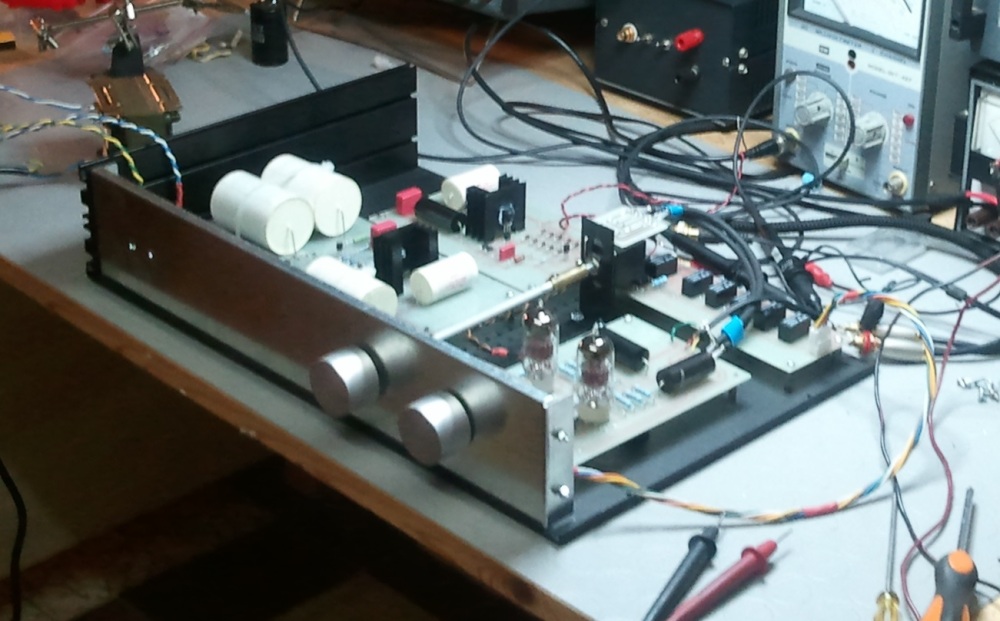
Una nota per il montaggio del potenziometro.
Il potenziometro l’ho posizionato il più vicino possibile agli ingressi. Per fare questo ho utilizzato una squadretta fissata al fondo del contenitore.
Poi mediante un giunto ho collegato l’alberino al pannello frontale. Qui la difficoltà maggiore l’avuta per allineare perfettamente il potenziometro alla boccola presente sul pannello frontale. L’alberino deve essere perfettamente allineato altrimenti la manopola scorre male e risulta essere “storta”.
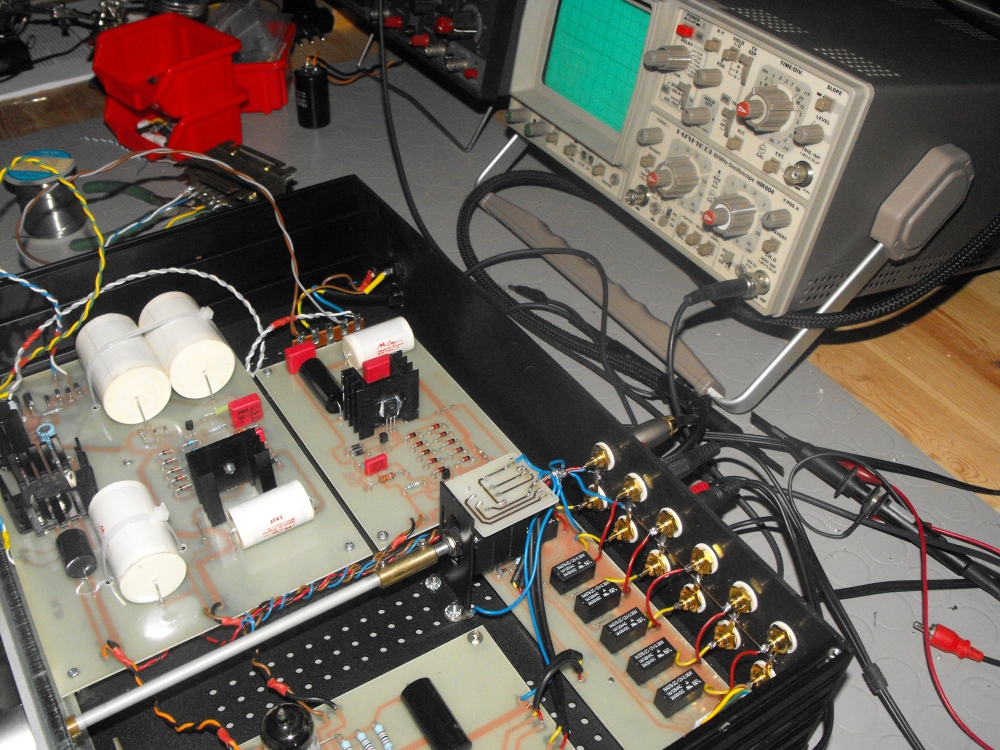
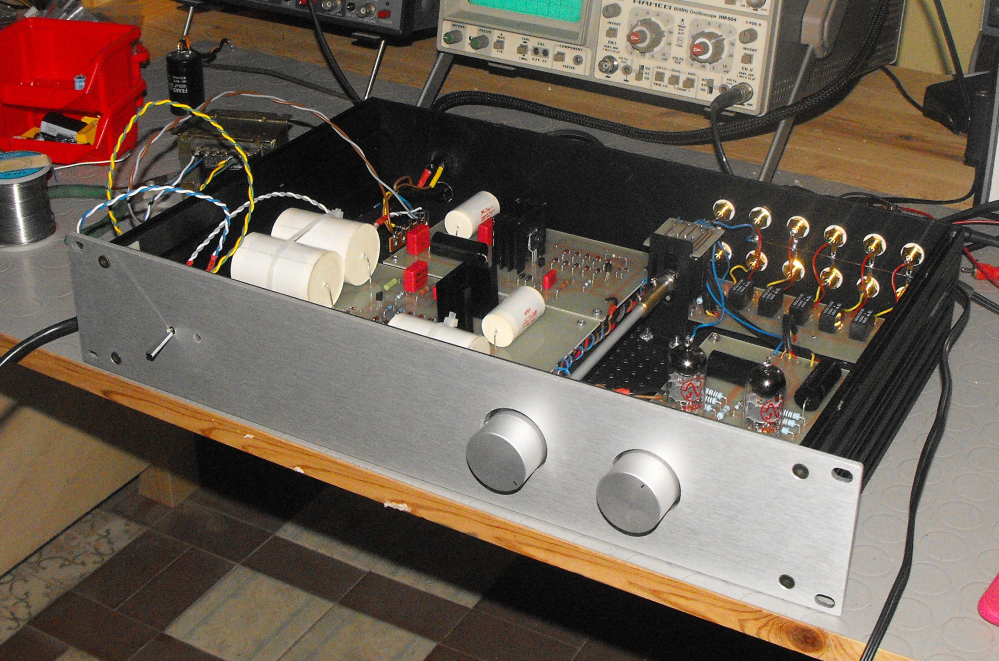
Finalmente è arrivato il trasformatore “custom“. Lo posso montare e finire il lavoro sul preamplificatore.
Per esso ho previsto il montaggio verticale nell’angolo sinistro posteriore, il più lontano possibile dai circuiti amplificatori e dagli ingressi.
Per il cablaggio ho “twistato” stretto i secondari e saldato il tutto sui circuito stampato principale dell’alimentatore. Ho poi fatto passare nella stessa zona i fili che collegano l’interruttore di alimentazione posto sul pannello frontale.
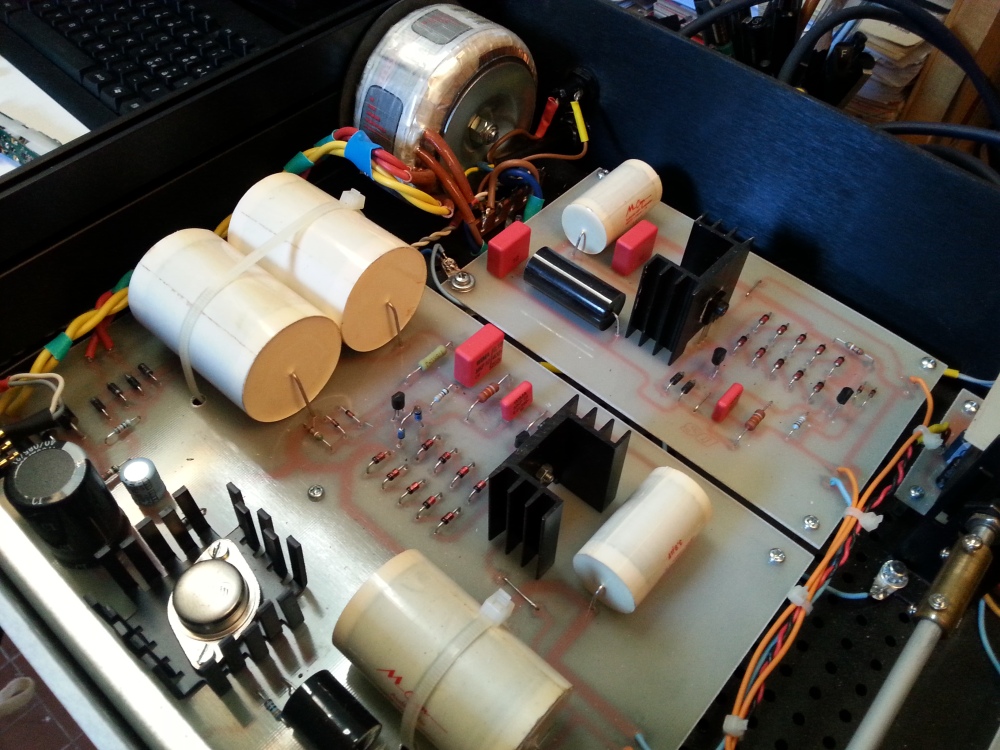
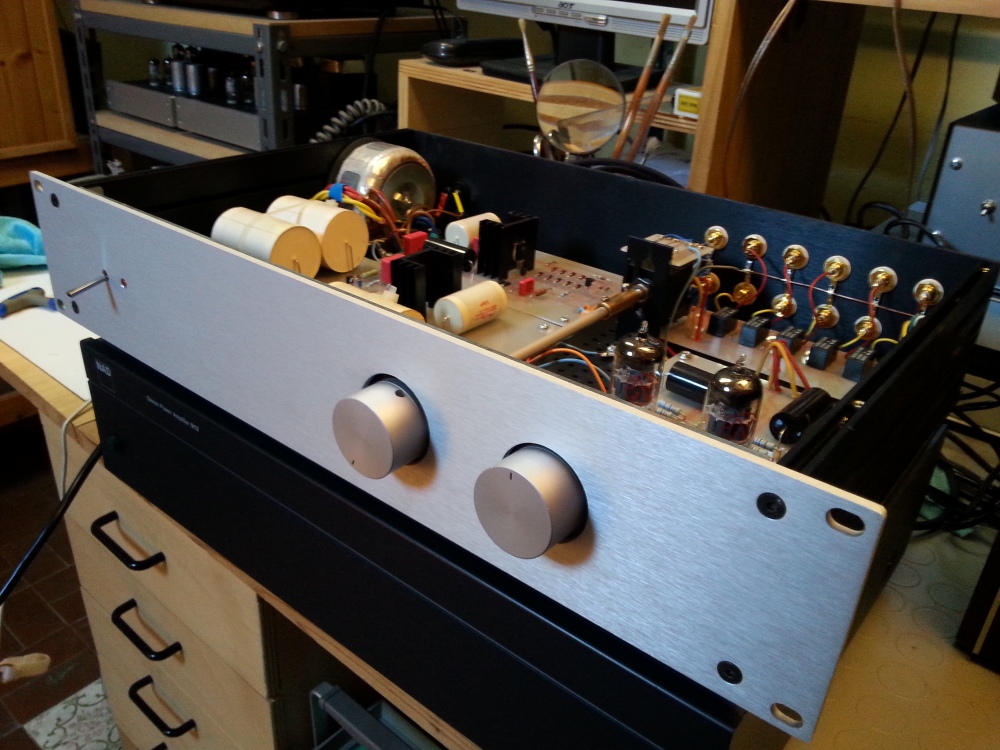
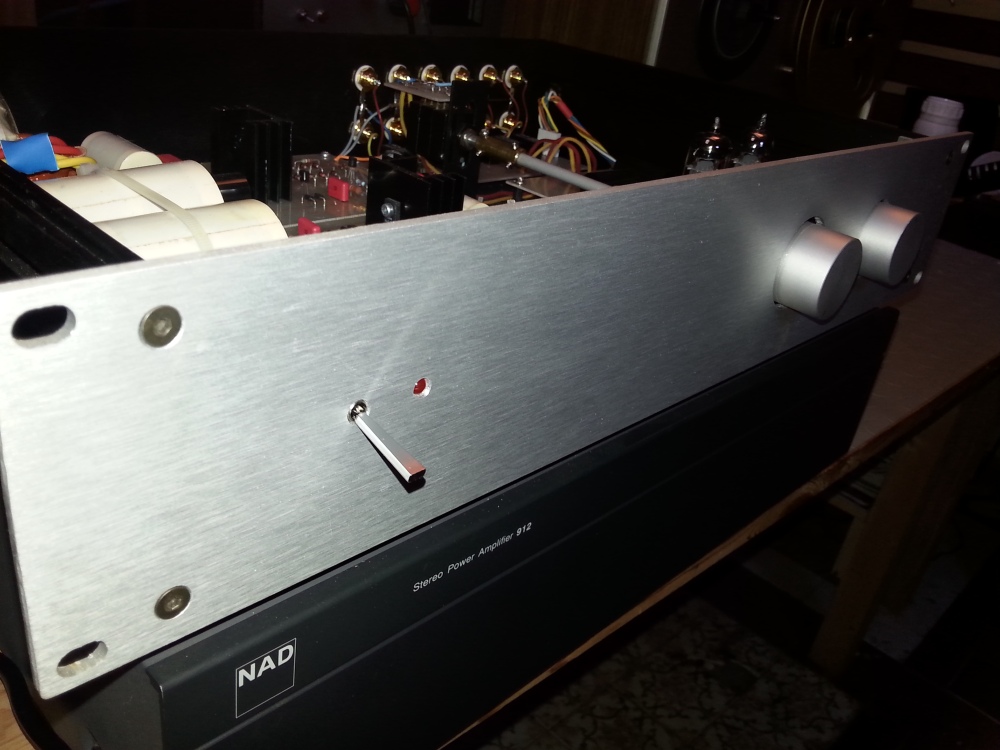
Conclusioni.
Il lavoro è stato complesso, per me, è durato circa quattro mesi. In questo progetto ho sperimentato nuove tecniche per la realizzazione di circuiti stampati e per la realizzazione del montaggio meccanico, e tante altre piccole cose utili alla nostra passione.
Per me è stata una bella esperienza, visto anche il buon suono che ne è risultato.
Buona costruzione a tutti…
Upgrade
Più che “upgrade” direi versione 2.0. E’ passato un po’ di tempo da quando ho realizzato il preamplificatore. L’articolo l’ho scritto ad ottobre 2016, ma il progetto risale al 2013. L’ho pubblicato adesso per avere memoria storica e raggruppare tutta la documentazione che ho del progetto, e soprattutto nel 2013 non avevo il blog e nemmeno pensavo di averne uno. Ma sapete com’è, i tempi cambiano…
Comunque il pre aveva dei difetti e adesso ho deciso di rimetterci le mani per migliorarlo ulteriormente. Una delle cose “fastidiose” che affliggeva l’apparecchio era un “tick” al cambio di sorgente.
Esso era provocato dalla mancanza dei diodi di protezione delle bobine dei relè. Questi diodi sono chiamati “spegniscintilla” e servono a limitare i disturbi generati della commutazione dei relè. Ho deciso quindi di montarli sotto la piastra in parallelo alle bobine dei relè. Ho quindi smontato il pannello posteriore, il potenziometro e liberato la scheda ingressi. Non avevo previsto questi diodi in fase di realizzazione del PCB, sicuramente una stata svista da neofita.
Comunque, è doveroso ringraziare gli amici del forum di Costruire Hifi per i loro consigli e spiegazioni tecniche.
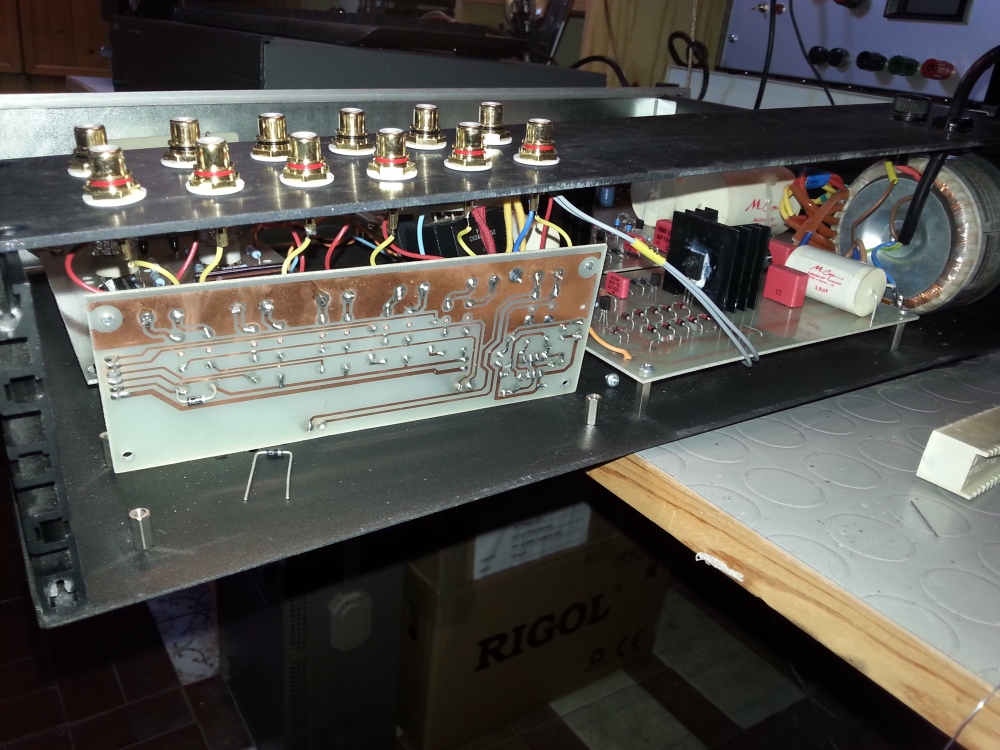
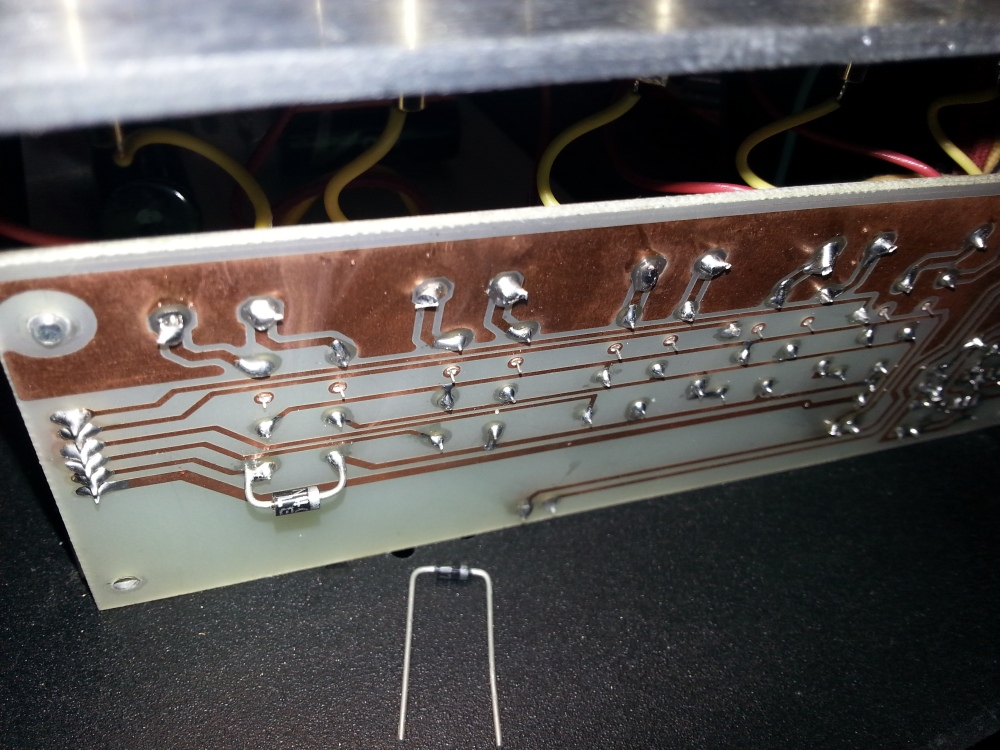
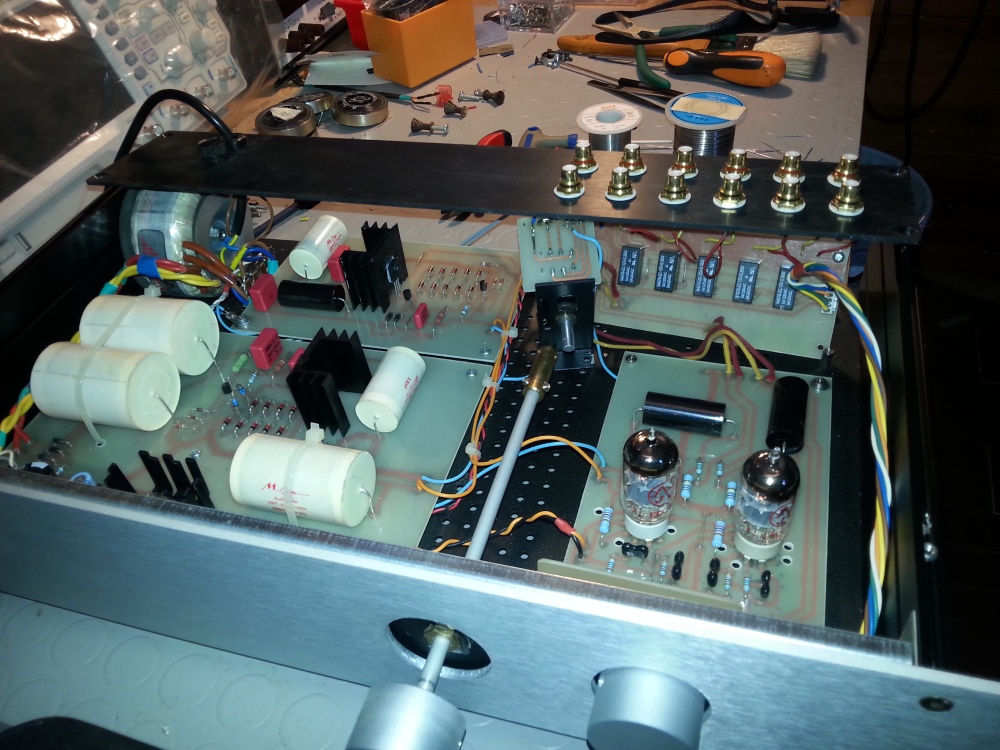
Modificata la scheda ho fatto subito un test per vedere se il problema era ancora presente.
Ho acceso l’apparecchio e collegato il finale, fatto il riscaldamento ho provato il selettore ingressi e, per “magia”, il fastidioso “tick” è sparito.
Ho colto l’occasione dello smontaggio della piastra per ricontrollare le saldature, ho anche controllato la schedina del potenziometro che aveva avuto diverse modifiche al volo in fase di test. Ne ho trovate alcune “sospette” che ho rinfrescato e ricontrollato per bene.
Ho rinforzato anche la parte 220v aggiungendo delle fascette e delle guaine termorestringenti. Questo per evitare dissaldature su tensioni pericolose.
Buon ascolto a tutti…
Devi effettuare l'accesso per postare un commento.